Plastic injection molding is a popular method used in the extensive field of manufacturing. It involves injecting molten plastic into a mold, followed by cooling and ejection to create complex and detailed plastic parts. These components are used across various industries, impacting their economic operations profoundly.
For instance, the health care sector heavily relies on this process to manufacture life-saving devices and intricate components. The automotive industry also finds value in plastic injection molding as it provides lightweight and durable materials.
Additionally, the consumer goods industry benefits greatly from its versatility and efficiency, offering a wide range of products including household appliances and toys. Behind this impressive manufacturing method lies a complex web of economic factors.
The costs of production, advancements in technology that improve efficiency, and shifting market trends all play vital roles in the economics of plastic injection molding.
This article aims to explore the economic aspects of plastic injection molding. By examining these factors, we to understand the significant impacts and potential future trajectories of plastic injection molding within the global economy.
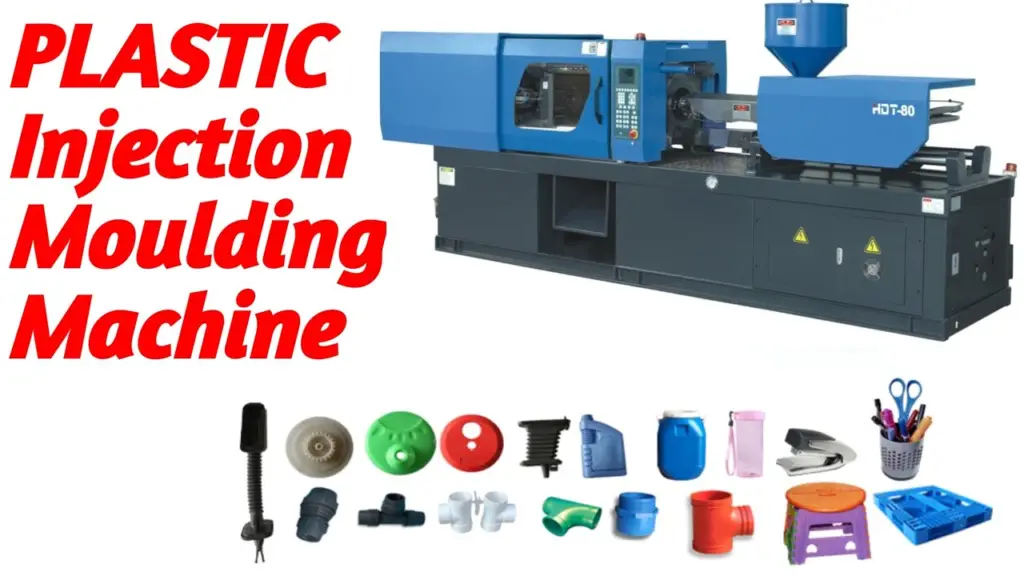
Cost Breakdown
Plastic injection molding is a capital intensive process with various costs involved in every step of the production process. Some of the main costs involved include the initial investment cost, material costs, labor costs and operational costs.
Initial Investment:
Plastic injection molding involves significant upfront set-up expenses, particularly related to molds and machinery.
Injection mold designs, typically crafted from steel or aluminum, can be quite costly due to their precise nature and the complexity of the parts they produce. Basic injection mold designs may range from a few thousand dollars, whereas more intricate designs could cost hundreds of thousands.
On the other hand, investing in machinery for injection molding requires a substantial capital outlay. The size, capacity, and features of the machine determine its price tag, which can vary from tens of thousands to well over a million dollars for advanced models.
Like Us on Facebook!
Material Costs:
The choice of plastic resins to use in plastic injection molding is essential. It determines both the final properties of the product and its overall cost. Different resins have varying prices, depending on their properties, origin, and demand-supply dynamics.
Subscribe Us on YouTube!
For example, common resins like polyethylene are relatively inexpensive, while specialized engineering plastics like PEEK (Polyether ether ketone) can be more costly.
Material costs can also be influenced by the volume of production and the weight of the final part.
Labor Costs:
Plastic injection molding involves the expertise of skilled engineers and technicians who handle machine operation, perform quality checks, and undertake post-processing tasks for molded parts.
In regions where labor costs are higher, this becomes a significant contributor to the overall cost structure. Additionally, expenses related to training, employee benefits, and safety measures further impact labor costs.
Operational Costs:
Running a plastic injection molding company entails various recurring expenses. One of the main operating costs is energy consumption, which arises due to the heating and cooling requirements of the process.
Additionally, regular machine and mold maintenance is necessary to ensure optimal performance and prolong their lifespan, but this also incurs additional costs. Apart from that, expenses related to quality control, waste management, facility rent, and utilities contribute significantly to the overall operational expenses.
Cost-Effectiveness and Efficiency
To be cost effective and efficient, there are some factors that manufacturers should consider. These include the economies of scale, speed and waste reduction.
Economy of Scale: One of the primary advantages of plastic injection molding lies in the economy of scale it offers. As the production volume increases, the average cost per unit starts to decrease.
Although there might be initial setup costs, particularly in mold creation, these expenses are divided among a large number of units during mass production. Consequently, when producing hundreds of thousands or even millions of parts, the per-unit mold cost becomes negligible, making this process highly cost-effective for large-scale production.
Speed: The injection molding process’s speed significantly contributes to its economic appeal. Once the initial setup is complete and the machine is running, it can produce parts in mere seconds to minutes. The production time depends on the size and complexity of the item.
This rapid turnaround enables manufacturers to produce large quantities within a short period, leading to faster time-to-market and quicker realization of revenues. Moreover, the process’s speed efficiently helps meet high-demand periods while consistently meeting supply chain needs.
Waste Reduction: Plastic injection molding is a precise process that emphasizes efficiency. By utilizing the exact amount of material needed for each part, wastage is minimized. Any leftover or excess material, like runners, can be recycled back into the process.
This not only saves costs but also promotes sustainability by reducing environmental impact. Manufacturers benefit economically as they maximize every kilogram of resin purchased through waste reduction.
Market Trends
With the rapid development in technology, plastic injection molding is facing rigouse advancements in various manufacturing sectors. In this section, we will explore the market trends that the industry is facing.
Growing Industries: The demand for plastic injection molding is increasing in various sectors. The healthcare industry, for example, heavily relies on this technology to produce medical devices, surgical tools, and disposables. This trend is driven by a growing global population and a greater emphasis on healthcare infrastructure.
Similarly, the automotive sector is using plastic components to meet lightweighting goals in automotive plastic injection molding, aiming to improve fuel efficiency and design electric vehicles. Additionally, in the ever-evolving consumer electronics industry, there is a high demand for top-quality plastic parts used in gadgets, wearables, and home appliances. Overall, injection molding offers immense growth opportunities across different sectors.
Technological Advancements: The landscape of plastic injection molding is undergoing a transformation through continuous technological advancements. Innovations such as computer-aided design (CAD) and computer-aided manufacturing (CAM) have revolutionized mold designs, reducing lead times and improving efficiency.
Automation and robotics have further streamlined the production process, enhancing precision and consistency while minimizing labor costs. Moreover, the emergence of Industry 4.0 technologies like IoT (Internet of Things) and AI (Artificial Intelligence) enable real-time monitoring, predictive maintenance, and optimized operational efficiencies. This convergence drives down expenses while elevating output quality to new heights.
Global Dynamics: The complex web of global supply chains greatly impacts the economics of plastic injection molding. When in search of cost-effective production, manufacturers often relocate or expand their operations to regions with lower labor costs.
However, this decentralization can pose challenges in quality control and add logistical complexities. Geopolitical tensions, trade wars, and pandemics have the potential to disrupt supply chains, making diversification and strategic location decisions essential for businesses operating in this industry.
Conclusion
In conclusion, plastic injection molding is a crucial production process in modern manufacturing involving various economic considerations.
From initial investments in molds and machinery to ongoing operational expenses, businesses entering this field must proceed with caution. It is essential for companies to conduct a thorough cost analysis and stay updated on market trends for successful outcomes.
If you are looking for a reliable partner to gain a competitive advantage in this intricate economic landscape, look no further than TDL Mold. This is a leading plastic injection molding company offering efficient plastic injection molding solutions customized to meet the industry demands.