In Civil Engineering and road construction, PQC stands for Pavement Quality Concrete. It is a M40 high quality concrete that is designed in accordance with IRC-15-2002 standard. In road projects, PQC is used as a top wearing layer for concrete roads. The thickness of such a wearing layer is generally from 180 mm to 300 mm.
In concrete or rigid pavement, the two important layers used are dry lean concrete (DLC) as a sub-base material and pavement quality concrete (PQC) as a wearing surface. Both the concrete types have zero slump value and have maximum aggregate-cement ratio.
The M40 mix design concrete being used as PQC has a characteristic compressive strength of 40 N/mm2.
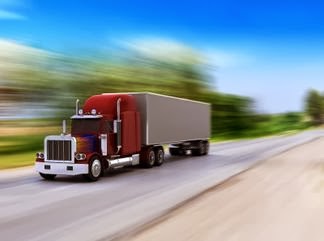
Specification and applications
Pavement Quality Concrete (PQC) is a high-strength concrete used for constructing rigid pavements. It is designed to withstand heavy loads and provide a durable surface for roads and airport runways.
- PQC is commonly used for rigid pavements, as it provides a strong surface that can withstand heavy traffic and impact loads.
- In addition to being used for roads, PQC is also used for construction of runways in airports. This is because the heavy impact load from airplane wheels needs to be distributed to the subgrade layers.
- Conventional normal grades concrete are not suitable for preparing PQC, it is recommended to develop M30 to M50 grade and more to achieve the requirements of PQC.
- To achieve higher strength, PQC is made with a lower water-cement ratio than conventional concrete. This results in a lower slump value, but a stronger final product.
- PQC is considered to be a high-performance concrete that provides a durable and long-lasting surface for roads and runways.
- PQC is also used for concrete road construction, rehabilitation, upgrading, modernization and resurfacing projects, to ensure the longevity and durability of the road surface.
- PQC is an important material in road infrastructure and building construction, it is an essential part of the pavement design and road surface layer.
- To maintain the high quality of PQC, it is important to adhere to the standards and specifications set out in IRC-15-2002, the standard for PQC in Indian Highways.
- PQC is a critical component of road and airport infrastructure, and its proper use and maintenance are crucial for ensuring safe and efficient transportation.
Procedure for Laying Concrete Road or Rigid Pavement
Alternate Panel Lying:
To avoid the development of shrinkage and thermal cracks, the concrete shall be laid in alternate panels. This method of laying the concrete in sections, rather than all at once, helps to minimize the potential for cracking caused by temperature changes and shrinkage.
Moisture Control:
To ensure that the concrete is not dried out prematurely, the base of the pavement shall be sprayed with water. This helps to keep the concrete at the appropriate moisture level during the curing process. Additionally, if specified in the drawing, a polythene sheet of 125 micron (with Lap of 300mm) shall be spread on the entire area to limit the loss of moisture from the concrete. The polythene sheet should be overlapped at the junctions to create a seal and prevent moisture loss.
Continuous Casting:
If continuous casting is desired, the same can be carried out with a saw cutting arrangement of the concrete pavement. This method allows for the concrete to be poured continuously, rather than in sections, which can help to improve the overall strength and durability of the pavement.
Saw Cutting:
Such pavement shall be cut to 1/3rd the depth at every 6m within 24 hours after laying the concrete. This process, known as saw cutting, helps to control the formation of cracks by creating joints in the concrete that allow for expansion and contraction. Any deviation in this time frame can result in irregular formation of cracks.
Final Inspection:
After all of the above steps are completed, the pavement should be inspected to ensure that it meets the specified standards and is ready for use. Any issues or defects should be addressed and corrected before the pavement is open to traffic.
Like Us on Facebook!
Construction and Expansion Joints for PQC
Placement of Stopper:
A typical construction joint consists of placing a stopper across the length and width of the pavement without affecting the spacing or placement of rebar. Necessary holes shall be made in the stopper to ensure proper alignment. All stoppers shall be applied with form release agents and removed as soon as the concrete attains its final set.
Subscribe Us on YouTube!
Surface Preparation:
To ensure a smooth finish, the concrete surface shall be made rough by chipping the same with a chisel immediately after de-shuttering. This process helps to create a better bond between the new and existing concrete and reduces the potential for cracking.
Expansion Joints:
For expansion joints, additional MS bar (Dowel Bar) shall be provided at half the depth of the pavement with 50% of the length of the rod in the previous concrete and the remaining in the next pour. Expansion joints of 25mm (or more) width and half of the depth of the pavement shall be provided after the required concrete length (as instructed in the drawing or technical specifications).
Construction Joints:
Construction joints of 12mm shall be provided after the required length. This helps to control the formation of cracks by creating joints in the concrete that allow for expansion and contraction.
MS Bar Insertion:
One end of the MS bar shall be coated with grease and covered in a plastic sleeve for easy movement. This helps to ensure smooth movement of the concrete during expansion and contraction.
Expansion Board:
If required as per drawing, an expansion board made of bitumen impregnated fibre or polystyrene shall be placed at the expansion joint area. This helps to provide additional support and stability to the joint.
Tie Bars Insertion:
Tie bars, as shown in the drawing, shall be inserted at the longitudinal joints where load transfer is minimal. This helps to transfer load across the joint, reducing the potential for cracking.
Final Inspection:
After all of the above steps are completed, the pavement should be inspected to ensure that it meets the specified standards and is ready for use. Any issues or defects should be addressed and corrected before the pavement is open to traffic.
Other Abbreviations