Saad Iqbal | đď¸Modified: March 22, 2018 | âłRead Time: 12 min | đPost Views: 1009
A pozzolana is a natural or artificial material containing silica in a reactive form. By themselves, pozzolanas have little or no cementitious value. However, in a finely divided form and in the presence of moisture they will chemically react with alkalis to form cementing compounds.
Fly ash has little cementing property when only water is added, its reactivity could be activated by OH [2,3], in ordinary Portland concrete, the pozzolanic reaction is very slow due to the low OH content. The replacement of part of cement and lime with fly ash in cementâlime mortar will consume a mass of calcium hydroxide (lime), at the same time the pozzolanic reaction will be activated due to the high OH content in mortars.Â
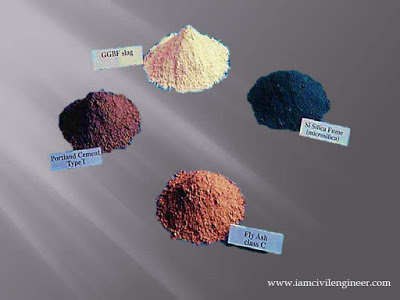 |
Use of Fly ash in Concrete & Its 11 impacts |
Content
Fly ash as Pozzolanic Material
Pozzolanas must be finely divided in order to expose a large surface area to the alkali solutions for the reaction to proceed.Â
Examples of pozzolanic materials are volcanic ash, pumice, opaline shales, burnt clay and fly ash.Â
The silica in a pozzolana has to be amorphous, or glassy, to be reactive.Â
Fly ash from a coal-fired power station is a pozzolana that results in low-permeability concrete, which is more durable and able to resist the entrance of deleterious chemicals.Â
The first reference to the idea of utilizing coal fly ash in concrete was by McMillan and Powers in 1934 and in subsequent researchÂ
When coal burns in a power station furnace between 1250°C and 1600°C, the incombustible materials combine to form spherical glassy droplets of silica (SiO2 ), alumina (Al 2O3 ), iron oxide (Fe2 O3 ) and other minor constituents.
Application of Fly ash in Construction
The positive effects while use of fly ash in concrete have resulted in numerous applications in construction industry due to sustainable and restorative approach towards deleterious effects.Â
In the construction sector, the fly ash is usedÂ
- in the production of cement as an additive-material,Â
- in production of concrete instead of some of the cement or instead of some of the fine aggregate
- as a base and sub-base material in highway construction
- as a filling material in dams, in retaining walls,Â
- for production of light construction materialsÂ
(ACI Committee 1987; Erdogan 1997).Â
Fly Ash and Pozzolanic ReactionÂ
When fly ash is added to concrete the pozzolanic reaction occurs between the silica glass (SiO2 ) and the calcium hydroxide (Ca(OH) 2) or lime, this is a by-product of the hydration of Portland cement. The hydration products produced fill the interstitial pores reducing the permeability of the matrix.Â
Roy (1987) states âthe reaction products are highly complex involving phase solubility, synergetic accelerating and retarding effects of multiphase, multi-particle materials and the surface effects at the solid liquid interfaceâ.Â
The reaction products formed differ from the products found in Portland cement-only concretes. A very much finer pore structure is produced with time presuming there is access to water to maintain the hydration process. Dhir et al. (1986) have also demonstrated that the addition of fly ash improves the dispersion of the Portland cement particles, improving their reactivity.Â
Little pozzolanic reaction occurs during the first 24 hours at 20°C. Thus for a given cementitious content, with increasing fly ash content, lower early strengths are achieved. Taylor (1997) explains the hydration processes involved in some detail.Â
The presence of fly ash retards the reaction of alite within the Portland cement at early ages. However, alite production is accelerated in the middle stages due to the provision of nucleation sites on the surface of the fly ash particles.Â
The calcium hydroxide scratches the surface of the glassy particles reacting with the SiO2Â or the Al2O3 âSiOÂ framework.Â
The hydration products formed reflect the composition of the fly ash with a low Ca/Si ratio.Â
Clearly the surface exposed for reaction is greater, the finer the fly ash; additionally, the higher the temperature, the greater the reaction rate.Â
At later ages the contribution of fly ash to strength gain increases greatly, provided there is adequate moisture to continue the reaction process.Â
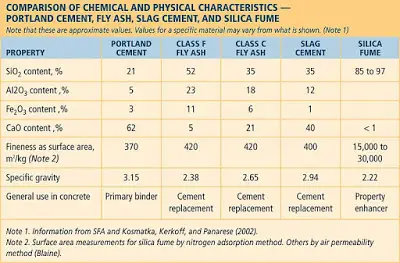 |
Comparison of Ordinary Concrete & Fly ash Concrete Chemical Properties (source)Â |
Effects of Using Fly ash in Portland Cement Concrete
In a normal concrete Calcium Hydroxide produced during hydration reaction is not put into much use. Whereas if we use fly ash, the fly ash will convert the CH into CSH. We know that CSH gel is the one responsible for the strength of the concrete.
The use of
fly ash in portland cement concrete (PCC) has many benefits and improves concrete performance in both the fresh and hardened state. Fly ash use in concrete improves the workability of plastic concrete, and the strength and durability of hardened concrete. Fly ash use is also cost effective. When fly ash is added to concrete, the amount of portland cement may be reduced.
All the effects of fly ash on properties of concrete are discussed in detail.Â
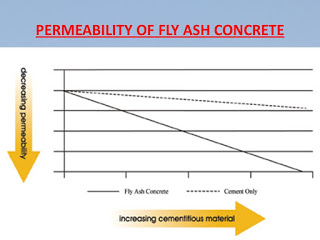 |
Permeability of Fly ash Concrete (Source: https://www.fhwa.dot.gov/pavement/recycling/fach03.cfm) |
You might also like to read :-Â
Reduced Heat of hydrationÂ
Due to increased replacement of fly ash with the proportion of cement in concrete mix design. Fly ash is able to reduce the heat of hydration very effectively.Â
The hydration of Portland cement compounds is exothermic. The introduction of fly ash to replace a proportion of cement in concrete influences temperature rise during the hydration period.Â
The rate of pozzolanic reaction increases with increasing temperature, however the peak temperatures in fly ash concrete are significantly lower than equivalent PC concretes.Â
Increased Setting Time & Form work Striking Time
Using fly ash in concrete will increase the setting time compared with an equivalent grade of PC concrete. There is a period before the hydration of fly ash concrete commences, but is has been shown by Woolley and Cabrera (1991) that the gain in strength, once hydration has started, is greater for fly ash concrete.Â
When 30 per cent fly ash is used to replace PC in a mix, the setting time may be increased by up to 2 hours.Â
This increased setting time reduces the rate of workability loss. However, it may result in finishing difficulties in periods of low temperature.Â
In compensation, it will reduce the incidence of cold joints in the plastic concrete.Â
Formwork striking times at lower ambient temperatures may have to be extended in comparison to PC concrete, especially with thin sections.Â
However, in practice vertical formwork striking times can be extended without this affecting site routines, e.g. the formwork are struck the following day. For soffit formwork, greater care has to be taken.Â
Better Elastic Modulus & Lower Creep
The elastic modulus of fly ash concrete is generally equal to or slightly better than that for an equivalent grade of concrete.Â
The greater long-term strength for fly ash concretes gives lower creep values, particularly under conditions of no moisture loss. These conditions may be found in concrete remote from the cover zone of a structure. Where significant drying is permitted the strength gain may be negligible and creep of OPC and fly ash concretes would be similar.Â
Lower Tensile strain capacity
Tensile strain capacity of
fly ash concretes has been found to be marginally lower, and these concretes exhibit slightly more brittle characteristics (Browne, 1984). There is possibly a greater risk of early thermal cracking for given temperature drop, partially offsetting the benefits of lower heat of hydration in the fly ash concrete.Â
Coefficient of thermal expansion
The type of coarse aggregate used largely influences the coefficient of thermal expansion of concrete. Replacement of a proportion of cement with fly ash will have little effect on this property (Gifford and Ward, 1982).Â
Effect of Fly ash on Curing
Hydration reactions between cement and water provide the mechanism for the hardening of concrete. The degree of hydration dictates strength development and all aspects of durability. If concrete is allowed to dry out hydration will cease prematurely. Fly ash concrete has slower hydration rates and the lack of adequate curing will affect the final product.Â
Thicker sections are less vulnerable than thin concrete sections because heat of hydration will promote the pozzolanic reaction.Â
Resistant to Alkaliâsilica reaction Effects
Alkaliâsilica reaction (ASR) (Concrete Society Technical Report 30, 1999) is potentially a very disruptive reaction within concrete. ASR involves the higher pH alkalis such as sodium and potassium hydroxides reacting with silica, usually within the aggregates, producing gel.Â
This gel has a high capacity for absorbing water from the pore solution causing expansion and disruption of the concrete. Some greywacke aggregates have been found particularly susceptible to ASR. The main source of the alkalis is usually the Portland cement or external sources.Â
Fly ash does contain some sodium and potassium alkalis but these are mainly held in the glassy structure and not readily available. Typically, only some 16â20 per cent of the total sodium and potassium alkalis in fly ash are water-soluble.Â
Many researchers have shown that fly ash is capable of preventing ASR. Oddly, the glass in fly ash is itself in a highly reactive fine form of silica. It has been found that the ratio of reactive alkalis to surface area of reactive silica is important in ASR.Â
The recommendations (BSI 5328 amendment 10365, 1999) within the UK require a minimum of 25 per cent BS 3892 Part 1 fly ash to prevent ASR. For coarser fly ashes, a minimum of 30 per cent fly ash may be required to ensure sufficient surface area to prevent ASR.Â
Small quantities of fine fly ash with low-reactivity aggregates and sufficient alkalis may be more susceptible to ASR if the pessimum silicaâalkali ratio is approached. Even when total alkalis within the concrete are as high as 5 kg/m 3 , fly ash has been found (Alasali and Malhotra, 1991) able to prevent ASR.Â
The addition of fly ash reduces the pH of the pore solution to below 13 at which point ASR cannot occur. The use of low-alkali cements has a similar effect.Â
Effects of Fly ash on Carbonation of concrete
As fly ash pozzolanically reacts with lime, this potentially reduces the lime available to maintain the pH within the pore solution. However, fly ash does reduce the permeability of the concrete dramatically when the concrete is properly designed and cured.Â
When designing concretes for equal 28-day strength the slow reaction rate of fly ash usually means that the total cementitious material is often increased. This increase partially compensates for the reduction in available lime. Coupling this with the lower permeability leads to the result that the carbonation of fly ash concrete is not significantly different from Portland cement-only concrete of the same grade (28 days)Â
Resistant to Freezeâthaw damage
Fly ash concrete of the same strength has a similar resistance to freezeâthaw attack as
Portland cement concrete. Dhir et al. (1987) reported on the freezeâthaw properties of concrete containing fly ash.Â
They used nine fly ashes of various sieve residues. All mixes were designed to give equal 28-day strengths. Freezeâthaw was assessed using an 8-hour cycle of 4 hours at â20°C and 4 hours at +5°C. Ultrasonic pulse velocity (UPV) and changes in length were used for the assessment of freezeâthaw performance.Â
They found, as have other researchers, that adding fly ash reduces freezeâthaw resistance unless air entrainment is used. However, Dhir found that only 1.0 per cent of air entrained in the concrete gave superior performance compared with plain concrete irrespective of the cement type.Â
It is clear that the less permeable and denser the mortar matrix is within the concrete, the less space is available to relieve the pressures associated with the expansion of freezing water.Â
Resistant to Sulfate attack
Fly ash concrete can increase the resistance to sulfate attack. Deterioration due to sulfate penetration results from the expansive pressures originated by the formation of secondary gypsum and ettringnite.Â
The beneficial effects of fly ash have been attributed to a reduction of pore size slowing penetration of sulfate ions. Less calcium hydroxide is also available for the formation of gypsum.Â
The smaller pore size of fly ash concrete reduces the volume of ettringnite that may be formed. One of the major constituents of cement that is prone to sulfate attack, tricalcium aluminate (C A), is diluted since a proportion of it will have reacted with the sulfates within the fly ash at an early age.Â