These are advanced machines that play a pivotal role in industrial manufacturing. These high-capacity machines enable businesses to produce plastic components efficiently and at a large scale. With their ability to handle high volume production demands, these moulders are essential for cost-effective manufacturing and meeting market demands across various industries. Their significance lies in streamlining production processes, ensuring consistent quality, and contributing to the overall efficiency of industrial manufacturing operations.
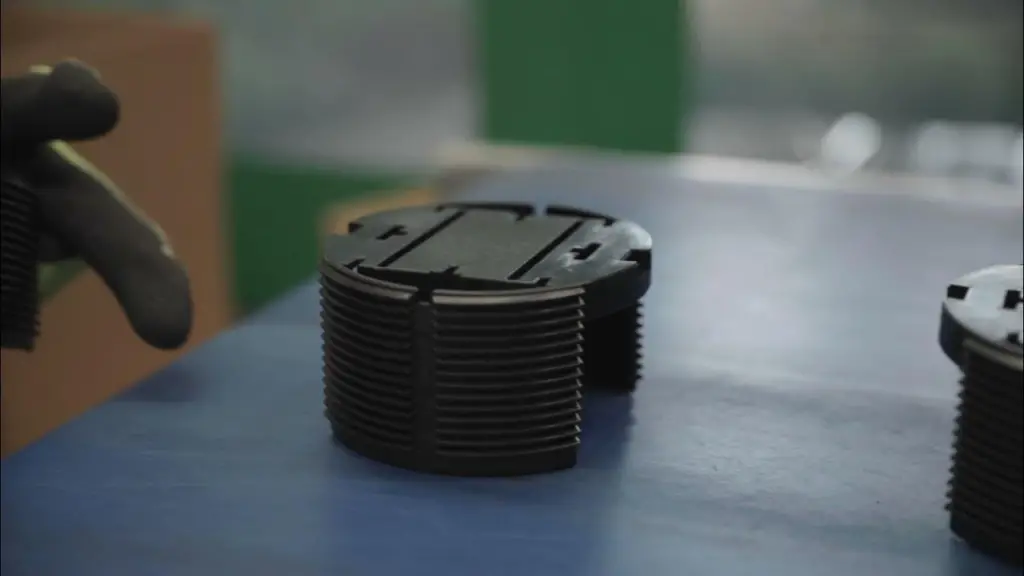
Industrial Manufacturing
Industrial manufacturing refers to the process of mass-producing goods on a large scale using advanced machinery and technology. These advanced machines are integral to this sector, as they enable efficient production of plastic components in high volumes. These machines contribute significantly to cost-effectiveness, consistent quality, and meeting the demands of various industries, making them crucial in modern industrial manufacturing processes.
Plastic Injection Moulding
Plastic injection moulding is a manufacturing process that involves injecting molten plastic into a mould to create various plastic components. Large scale injection moulders are key players in this technique, as they enable mass production of plastic parts with efficiency and precision. This method finds wide applications across industries, showcasing its significance in modern manufacturing processes.
Also Read: The Importance of Explosion Proof Lights for Electrical Contractors
High Volume Production
High volume production is a critical aspect of industrial manufacturing, and These high-capacity machines are instrumental in achieving this feat. These machines possess the capacity to produce a significant number of plastic components within short time frames, making them indispensable for businesses with substantial production demands. Their ability to handle large quantities efficiently ensures cost-effectiveness, streamlined processes, and meeting market demands, emphasizing their significant role in modern industrial manufacturing operations.
Injection Molding Machine
An injection molding machine is the core equipment used in large scale injection moulding. It operates by injecting molten plastic into a mould to create various plastic components. These machines are vital in industrial manufacturing as they enable mass production, cost-efficiency, and consistent quality control. The significance of injection molding machines lies in their ability to meet the demands of high volume production and their wide applications across industries.
The Advantages of Using Large Scale Injection Moulders in Industrial Manufacturing Processes
High Production Output
High production output is a significant advantage of using moulders in industrial manufacturing. These machines can produce a large number of plastic components within a short period, meeting high volume production demands efficiently. The increased output translates to faster turnaround times, enabling businesses to meet tight deadlines and respond to market demands swiftly. Additionally, high production output contributes to cost-effectiveness, reducing per-unit costs and maximizing overall productivity.
Also Read: Drilling Equipment: Advanced Construction Technology
Cost Efficiency
Cost efficiency is a key advantage of moulders in industrial manufacturing. By streamlining production processes and producing high volumes of components, these machines minimize per-unit costs, resulting in significant cost savings. Economies of scale and optimized material usage further enhance cost efficiency, making them moulders a cost-effective choice for businesses.
Like Us on Facebook!
Consistent Quality
Consistent quality is a major advantage of large scale injection moulder. These machines ensure uniform part dimensions, tight tolerances, and precise replication, guaranteeing reliable and standardized product outputs. Maintaining consistent quality is vital in meeting industry standards and customer expectations in industrial manufacturing processes.
Subscribe Us on YouTube!
Rapid Production Cycles
Rapid production cycles are a significant advantage in industrial manufacturing. These efficient machines enable quick injection of molten plastic into moulds, reducing production times. Faster cycles contribute to meeting tight deadlines, accommodating high-volume orders, and responding promptly to market demands. Rapid production ensures businesses can stay competitive and fulfill customer needs efficiently.
Versatility In Material Selection
Versatility in material selection is a key advantage in industrial manufacturing. These machines can work with a wide range of plastic materials, including thermoplastics and elastomers, providing flexibility in product design and applications. The ability to choose from various materials allows businesses to create diverse products with different properties, meeting specific industry requirements and customer preferences.
1. Increased Production Output And Efficiency
Increased production output and efficiency are critical advantages in industrial manufacturing. The use of high-capacity moulding machines and faster cycle times enable businesses to produce a higher volume of plastic components in less time. This enhanced efficiency not only reduces production costs but also maximizes productivity, allowing manufacturers to meet large-scale production demands effectively and stay competitive in the market.
2. Cost Efficiency and Reduced Material Waste
Cost efficiency and reduced material waste are essential benefits in industrial manufacturing. The concept of economies of scale allows businesses to optimize material usage, minimizing scrap and rework costs. By maximizing material efficiency, companies can significantly reduce production expenses, making the manufacturing process more financially sustainable and environmentally friendly.
3. Consistent Quality and Precise Replication
Consistent quality and precise replication are paramount in industrial manufacturing. The tight tolerances and quality control techniques employed ensure uniform part dimensions and surface finish, resulting in reliable and standardized product outputs. Maintaining consistent quality is essential for meeting industry standards and customer expectations, while precise replication allows businesses to reproduce intricate designs and complex geometries with accuracy and reliability.
The Future of Large Scale Injection Moulding: Technological Advancements & Innovations
The future of large scale injection moulding holds exciting possibilities with technological advancements and innovations. Automation integration is expected to streamline the production process further, reducing the need for manual intervention and increasing efficiency. Data-driven optimization will play a crucial role in real-time adjustments and process improvements, leading to enhanced cost-effectiveness and faster production cycles. These advancements in large scale injection moulders will revolutionize industrial manufacturing, meeting the demands of a dynamic and evolving market.
Trends such as automation integration
Trends such as automation integration are shaping the future of injection moulding. Advanced automation technologies will streamline manufacturing processes, increasing efficiency and reducing human intervention. This integration allows for faster production cycles and improved productivity, enhancing cost-effectiveness and making injection moulding a more attractive option for businesses seeking to stay competitive in the evolving manufacturing landscape.
Data-Driven Optimization To Increase Efficiency
Data-driven optimization is a crucial aspect of the future of injection moulding. Utilizing data analytics and real-time monitoring, manufacturers can identify areas of improvement and optimize production processes for enhanced efficiency. By making data-informed decisions, companies can reduce costs, minimize downtime, and achieve higher productivity, positioning themselves to thrive in the ever-evolving landscape of industrial manufacturing.