In the dynamic realm of modern manufacturing, the quest for efficiency and precision has led to the evolution of various machining tools. Among these, live tooling stands out as a game-changer. Unlike traditional static tools, live tool holders bring versatility and agility to CNC lathes, allowing them to perform multiple operations seamlessly. This transformative capability not only streamlines the production process but also elevates the quality and precision of the final product. As industries continue to seek innovative solutions to meet growing demands, the significance of live tooling in today’s manufacturing landscape cannot be overstated.
Check the toolholdernow for both live and static tool holders
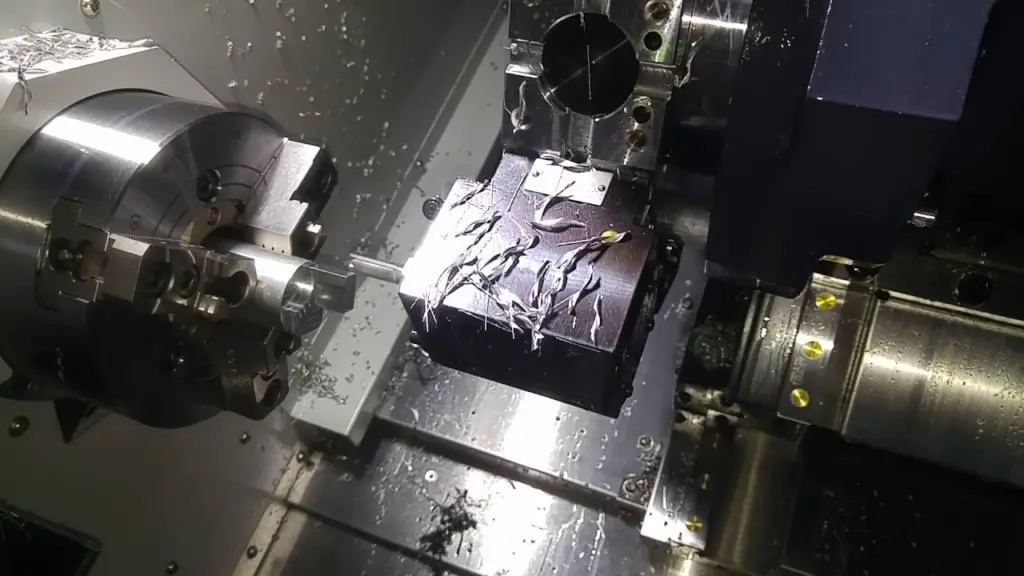
What is Live Tooling?
Live tooling refers to the integration of rotating tools into CNC lathes, enabling these machines to perform operations like drilling, milling, and tapping while the workpiece remains stationary. Historically, traditional lathes were limited to turning operations, where the workpiece rotated while the tool remained static. However, as manufacturing needs evolved, so did the machinery. The advent of CNC technology brought about the fusion of milling centers and lathes, giving birth to CNC lathes with live tooling capabilities. This evolution marked a significant leap, offering manufacturers unparalleled versatility and efficiency in their machining processes.
Key Benefits of Live Tooling
The integration of live tooling in CNC lathes has revolutionized the manufacturing industry. This innovation offers a plethora of advantages that cater to the ever-evolving demands of modern production. Here’s a deep dive into the key benefits of live tooling:
1. Enhanced Efficiency and Speed
The modern manufacturing landscape demands speed without compromising on quality. Live tooling, with its advanced gears and bearings, facilitates faster fabrication, significantly reducing production time. Moreover, the ability to perform multiple operations without the need to change setups or machines means fewer interruptions and quicker job completion. This efficiency is a boon for industries where time is of the essence.
2. Precision and Accuracy
Accuracy is paramount in manufacturing. Live tooling minimizes human errors, ensuring that each part produced meets the desired specifications. The consistent quality of parts is further enhanced by the ability to maintain datum, ensuring that reference points remain unchanged throughout the machining process. This precision translates to fewer rejections and higher customer satisfaction.
3. Versatility in Manufacturing
Live tooling’s versatility is one of its standout features. A single machine can seamlessly transition from turning operations to drilling, tapping, boring, and even milling. This means that complex parts, which previously required multiple machines and setups, can now be fabricated within a single setup, streamlining the entire production process.
4. Cost and Time Savings
The financial implications of live tooling are profound. The reduction in setup and handling time translates to significant cost savings. Additionally, the elimination of time-consuming part transfers, often between different machines, further reduces production time. This efficiency not only saves money but also allows manufacturers to meet tight deadlines and cater to larger order volumes.
5. Improved Quality Control
Quality control is at the heart of manufacturing. Live tooling, with its reduced human interaction, inherently leads to fewer errors. The automated processes ensure that each part produced adheres to the set standards, ensuring consistent output. This consistency is crucial, especially in industries where even the slightest deviation can have significant implications. With live tooling, manufacturers can be confident in the quality of every part that comes off the production line.
Like Us on Facebook!
Potential Applications of Live Tooling
Live tooling has ushered in a new era of versatility in manufacturing, enabling CNC lathes to perform a wide range of operations that were once confined to specialized machines. Here’s a closer look at the potential applications of live tooling:
Subscribe Us on YouTube!
1. Milling
Milling is a subtractive process where material is removed from a revolving workpiece to achieve the desired shape or finish. With live tooling, CNC lathes can seamlessly transition to milling operations, allowing manufacturers to shape, contour, and refine parts without the need for a separate milling machine, thus optimizing the production process.
2. Boring
Boring is the precision enlargement of already drilled holes. Live tooling enhances this process by ensuring that the enlargement is accurate and consistent. Whether it’s to fit a specific component or to improve the surface finish inside a hole, live tooling ensures that boring operations meet the exacting standards required in modern manufacturing.
3. Drilling
Drilling involves creating cylindrical holes in a workpiece. With live tooling, these holes can be drilled with precision, ensuring they are perfectly positioned for joining components or for other assembly requirements. The ability to drill while the workpiece remains stationary ensures that holes are accurately placed, reducing errors and wastage.
4. Tapping
Tapping is the process of cutting threads inside holes or slots, allowing for the insertion of screws or other threaded components. Live tooling brings efficiency to tapping, ensuring that threads are cut accurately and consistently. This precision is crucial for ensuring the structural integrity of assembled parts and products.
5. Turning
Turning involves cutting material from the external diameter of a rotating workpiece. While traditional lathes were primarily used for turning, live tooling elevates this process. It allows for intricate cuts, grooves, and finishes to be made on the external surface, ensuring that the workpiece is shaped and sized to exact specifications, ready for its intended application.
FAQs
1. What is the difference between static and live tooling?
Static tooling remains stationary during operations, while live tooling rotates and can perform multiple tasks like drilling and milling without changing the setup or the workpiece’s position.
2. How does live tooling enhance CNC lathe capabilities?
Live tooling transforms CNC lathes into versatile machines, enabling them to perform turning, drilling, tapping, and milling operations seamlessly within a single setup, optimizing production processes.
3. Are there any limitations to using live tool holders?
While live tool holders offer versatility, they require precise setup and calibration. Additionally, they might be overkill for simple tasks and can be costlier than static tooling.
4. How does live tooling contribute to cost savings in manufacturing?
Live tooling reduces setup times, eliminates the need for multiple machines, and streamlines operations, leading to faster production, reduced labor costs, and minimized wastage.
5. What industries benefit the most from live tooling?
Aerospace, automotive, medical, and electronics industries, where precision and multifaceted machining are crucial, greatly benefit from the versatility and efficiency of live tooling.
Conclusion
In the ever-evolving landscape of modern manufacturing, live tool holders have emerged as indispensable assets. They seamlessly integrate multiple operations, ensuring precision, efficiency, and versatility. From reducing production times to enhancing the quality of the final product, the benefits they offer are manifold. As industries continue to push the boundaries of innovation, the role of live tool holders remains pivotal, underscoring their significance in shaping the future of manufacturing.